前回、不適合(欠点)数の管理図である\(c\)管理図の作り方を解説しました。
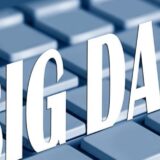
\(c\)管理図では不適合の現れる大きさが一定の製品や工程に対して、不適合数を打点しましたが、不適合の現れる大きさが一定でない製品や工程の不適合数を管理したい場合があります。
そのときに有効な管理図が\(u\)管理図です。
\(u\)管理図は単位当たりに換算した不適合数を打点する管理図で、不適合の現れる大きさが一定でなくても構いません。
今回の記事では、\(u\)管理図の作り方を解説します。
1. \(u\)管理図とは
\(u\)管理図は、単位当たりの不適合(欠点)数をプロットする管理図です。
不適合が現れる範囲は一定である必要はありません。
例えば、長さの異なるホースを数種類作っている工程で、長さ1m当たりのキズの数をプロットするといった場合です。
\(p\)管理図と同じく、サンプルの大きさによって管理限界の幅も変わってしまうデメリットがあります。
2. \(u\)管理図の作り方
手順1 データを取る
サンプル中に1~5個程度の不適合品が含まれるような大きさのサンプルを20~25群取り、サンプルを検査して不適合数を調べます。
手順2 単位当たりの不適合数\(u\)を計算する
各群の単位当たりの不適合数\(u\)を計算します。
\(u=\displaystyle \frac{c}{n}\)
ただし、
\(c\):サンプル中の不適合数
\(n\):サンプルの大きさ
手順3 管理線を計算する
管理線として中心線(CL)、上方管理限界線(UCL)、下方管理限界線(LCL)を計算します。
\(u\)管理図 | |
---|---|
CL | \(\bar{u}=\displaystyle \frac{\sum c}{\sum n}\) \(\sum c\):不適合品数の合計 \(\sum n\):サンプル大きさの合計 |
UCL | \(\bar{u}+3 \sqrt{\displaystyle \frac {\bar{u}}{n}}\) |
LCL | \(\bar{u}-3 \sqrt{\displaystyle \frac {\bar{u}}{n}}\) ※値がマイナスになる場合、LCLは考えない。 |
手順4 管理図に記入する
単位当たりの不適合数\(u\)を縦軸に、群の番号を横軸に目盛り、各群の不適合数を打点します。
さらに、手順3で求めた中心線、UCL、LCLを数値とともに記入します。
通常、中心線は実線、UCLとLCLは破線を用います。
サンプルの大きさが各群で異なる場合は、管理限界線は中心線に対して凸凹になります。
手順5 管理状態にあるかを判定する
3. \(u\)管理図の作成例
20群のデータの例を使って、\(u\)管理図を作成してみましょう。
手順1~2
No | サンプルサイズ | 不適合品数 | \(u\) |
---|---|---|---|
1 | 1.4 | 5 | 3.57 |
2 | 1.4 | 0 | 0 |
3 | 1.4 | 4 | 2.86 |
4 | 1.4 | 3 | 2.14 |
5 | 1 | 3 | 3.00 |
6 | 1 | 4 | 4.00 |
7 | 1 | 6 | 6.00 |
8 | 1 | 1 | 1.00 |
9 | 1.8 | 5 | 2.78 |
10 | 1.8 | 8 | 4.44 |
11 | 1.8 | 9 | 5.00 |
12 | 1 | 2 | 2.00 |
13 | 1 | 4 | 4.00 |
14 | 1 | 3 | 3.00 |
15 | 0.6 | 4 | 6.67 |
16 | 0.6 | 1 | 1.67 |
17 | 0.6 | 3 | 5.00 |
18 | 2 | 13 | 6.50 |
19 | 2 | 8 | 4.00 |
20 | 2 | 7 | 3.50 |
合計 | 25.8 | 93 |
手順5 管理線の計算
\(u\)管理図 | |
---|---|
CL | \(\bar{u}=\displaystyle \frac{\sum c}{\sum n}=\displaystyle \frac{93}{25.8}=3.60\) |
UCL | 下表参照 |
LCL | 下表参照 |
No | UCL | LCL |
---|---|---|
1 | 8.41 | |
2 | 8.41 | |
3 | 8.41 | |
4 | 8.41 | |
5 | 9.29 | |
6 | 9.29 | |
7 | 9.29 | |
8 | 9.29 | |
9 | 7.84 | |
10 | 7.84 | |
11 | 7.84 | |
12 | 9.29 | |
13 | 9.29 | |
14 | 9.29 | |
15 | 10.95 | |
16 | 10.95 | |
17 | 10.95 | |
18 | 7.62 | |
19 | 7.62 | |
20 | 7.62 |
※LCLの空白部分は、マイナスの値だったことを示す。(本事例ではすべてマイナス)
手順4 管理図に記入
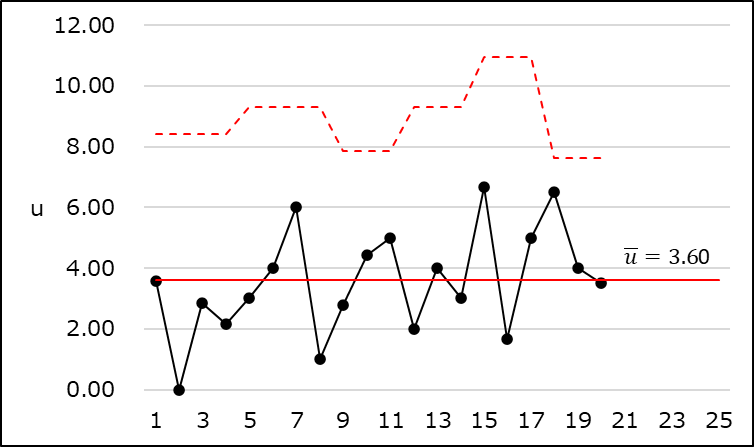
市販の書籍を見ると\(u\)管理図の管理限界線は矩形波で書かれていますが、Excelで矩形波を表示するのは大変なので、一般的な折れ線グラフで表示しています。
手順5 管理状態の判定
打点は管理限界を越えておらず、連など特に傾向も見られないことから、工程は管理状態にある判定できます。
4. おわりに
今回は、\(u\)管理図の作り方を解説しました。
サンプルの大きさが一定でないため、\(c\)管理図と違って管理限界がサンプルの大きさによって異なるという特徴があります。